Where limited building space and/or limited transportation means make it impossible
to build large boats "in one piece" there are only two alternatives:
Give up and stick with small boats, or build that large dream boat in modules.
In Vietnam, we are not known for giving up, but to master seemingly impossible tasks
by determination and ingenuity, using all available means, as simple as they may look,
to achieve the final goal. So, what about building a large boat out of small modules
that can be built in small rooms and be transported with small vans?
A study of the forces that get bigger the bigger the boat gets, shows that the main problem
stems from large waves: With the right wave length, the bow and stern of the boat might be lifted,
while the middle part is suspended between. In another scenario, a large wave amidships would lift
bow and stern out of the water. The result are forces (boyance of the waves, weight of the ship)
that try to bend a flat bottom up and downwards. If the forces are handled by vertical sides,
then it results there in longitudinal forces: compressive and tensional load
at the upper and lower edge of the sides, with a neutral line (i.e. no forces there)
somewhere in between.
The main challenge for a modular construction is how to handle those forces accross the
single modules.
How are forces handled in other modular constructions? Let's have a look at a system,
that many of us probably know: The Lego© toy bricks. With those bricks one can assemble
very large structures out of comparably tiny building blocks. And while the structures can be
quite strong, the single modules are attached to each other only in a single dimension,
where the "sticking force" is even quite moderate. Like any other non-compressible
material (including wood), the Lego bricks can handle compressive loads well.
No need to consider them. The problematic and therefore interesting forces are tensile stresses.
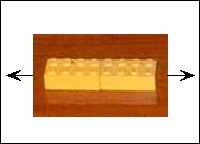
Connection 1:
Strong constructions can be assembled, although the bricks cannot handle any force
in this direction!
|
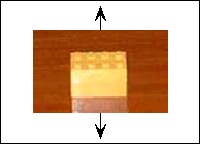
Connection 2:
They can handle some, although not too much force in this direction.
|
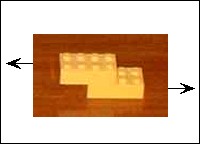
Connection 3:
This is where the real strength lies!
|
How does this look now in our application, i.e. strengthening and stiffening a flexible bottom?
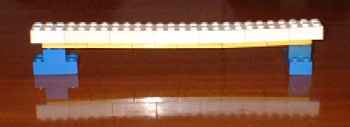
Large waves at bow and stern leave the middle suspended. It bends somewhat,
though maybe acceptable.
In a boat this could be reduced by bolting the bottom modules together across the beam.
|
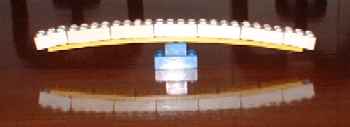
The single wave midships creates a big problem. Bow and stern bend downwards.
In a boat very little could be done against it.
|
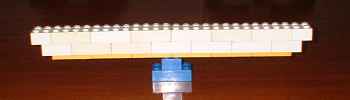
As soon as we add a second layer of modules, the arrangement becomes very stiff,
even in the situation with a single wave midships.
The trick, of course, lies in mounting the different layers shifted by a half module.
If they would be mounted exactly on top of each other, one would gain little.
|
The considerations above make the weak points in the
TIMS assembly obvious:
It consists of a single layer of modules, and a few bolts at the bulkheads have to hold
everything together.
The bolts, and via them the bulkheads, are loaded with tensile stress and cannot take much force,
similar to the Connection 2 above.
Larger waves would get it most probably in serious trouble.
But what if we assembled a boat like the double-layer brick construction above?
Look at a construction like that:
The bulkheads of the bottom float modules would extend to well obove the waterline, like in the TIMS.
The side panels need to be connected to each other and to bottom and roof with bolts
only on top and bottom, like the Lego brick assembly above. The easiest to do this might be
with flat steel bars at the inside or outside, overlapping the edges for a few inches
from below to above. Another way would be to bolt directly by overlapping the panels
like in a lapstrake construction.
The bolted connections are not stressed for tension, but similar to the Lego bricks
in Connection 3 above. If wood is used at the edges of the panels, or the extra bars,
one has to take care that thin bolts don't split the logs, e.g. by tightening the bolts strong enough
that the forces are taken by friction (and for permanent connection by glue) along the logs.
The construction can be made watertight with silicone construction glue in the small gaps,
and adhesive tape or adhesive foils outside. If the bottom float modules are made watertight,
then a self-draining cockpit could be made, and watertight connections between the panels
become less of an issue. To provide lateral stiffness, the side panels are preferably made of
"foam sandwiches" with thin layers of plywood or sheet metal outside and inside.
The result is, that large river sharpies with several dozen feet length could be assembled of
modules that are only one inch (side panels) to about one foot (bottom float modules) thick
and thus can be transported very easily.
|